General
A Guide to Choosing Mica Band Heaters for Injection Molding Machines
Getting the right mica band heater for an injection molding machine isn’t just about finding one that fits. It’s about choosing the right watt density, material compatibility, and installation features to ensure maximum efficiency and longevity. A well-selected mica band heater keeps operations running smoothly while reducing maintenance costs over time.
Selecting Optimal Watt Density for Superior Performance
Watt density plays a critical role in how effectively a mica band heater transfers heat to the injection barrel. Too low, and the heater may struggle to maintain proper temperature, leading to inconsistent molding results. Too high, and it could overheat, reducing the lifespan of both the heater and the machine components. Finding the balance ensures the heater runs efficiently without premature failure.
When selecting a mica band for injection molding, the watt density should match the specific heat requirements of the material being processed. High-performance resins often require heaters with higher watt density to maintain the necessary temperatures without excessive cycling. On the other hand, lower watt densities can be ideal for materials that heat more easily, ensuring steady performance without energy waste. Choosing the right watt density can make a significant difference in productivity and the overall quality of molded parts.
Material Compatibility Ensuring Maximum Heater Efficiency
Not all mica band heaters are created equal, and the materials used in their construction directly impact their efficiency. The outer sheath, typically made of stainless steel or brass, determines how well the heater withstands environmental conditions and physical wear. Stainless steel sheathing is highly resistant to corrosion, making it ideal for humid or high-moisture environments, while brass offers superior heat conductivity, allowing for faster heat transfer.
The inner insulation layer, usually composed of mica, plays a key role in heat retention. High-quality mica ensures even heat distribution while preventing electrical leakage. Choosing a heater with superior mica insulation minimizes heat loss and improves energy efficiency. By selecting a mica band with the right combination of sheath and insulation materials, manufacturers can extend heater life and reduce energy consumption while maintaining precise temperature control.
Heater Diameter Accuracy to Prevent Heat Loss and Downtime
A properly sized mica band heater makes all the difference in heat transfer efficiency. If the heater is too loose around the barrel, heat escapes, forcing the unit to work harder and consume more energy. If it’s too tight, it can crack or become damaged during installation, leading to premature failure. Accurate diameter measurement ensures the heater maintains consistent contact with the barrel surface, optimizing performance.
Even minor deviations in size can cause uneven heating, resulting in hotspots that may affect plastic flow inside the injection barrel. Measuring carefully before purchasing a mica band prevents these issues. Additionally, selecting a heater with flexible construction allows for better conformity to the barrel’s surface, reducing thermal gaps and improving overall efficiency. Investing in precise sizing ultimately leads to fewer replacements and less downtime.
The Impact of Terminal Choices on Installation Simplicity
Terminal placement and type significantly affect how easy it is to install and replace a mica band heater. Side terminals are convenient for compact spaces, while post terminals provide flexibility in wiring. Some heaters offer screw terminals for secure connections, while others use quick-connect options for faster installation and maintenance.
Poor terminal placement can make installation cumbersome, leading to extended downtime during heater replacements. Choosing a mica band with terminals positioned for easy access streamlines maintenance and prevents unnecessary disruptions. Properly secured terminals also reduce the risk of electrical failure, ensuring reliable operation throughout the heater’s lifespan. Selecting the right terminal configuration can simplify both initial setup and future replacements.
Protective Features That Guard Against Operational Failures
Mica band heaters endure intense heat cycles, and without proper protective features, they can wear out quickly. Built-in thermal insulation reduces heat loss and prevents damage from overheating. Some heaters include protective coatings or stainless steel jackets to shield them from contaminants like oil, dust, or moisture.
Moisture-resistant coatings are especially beneficial in humid environments, preventing electrical shorts and extending heater life. Additionally, built-in strain relief features help prevent wire breakage from frequent machine movement. These protective elements contribute to longer heater durability and reduce the likelihood of sudden operational failures, keeping production lines running efficiently.
Evaluating Heater Thickness for Faster Heat Transfer and Durability
The thickness of a mica band impacts how quickly and evenly heat is transferred to the injection barrel. Thicker bands retain heat longer, making them more energy-efficient for extended operation, while thinner bands respond more quickly to temperature adjustments, providing better precision for sensitive molding processes.
Balancing thickness with durability is essential for long-term performance. If a heater is too thick, it may take longer to reach operating temperature, leading to slower cycle times. However, a heater that is too thin may degrade faster under continuous high-heat conditions. Choosing a mica band heater with an optimized thickness ensures fast heat transfer while maintaining structural integrity, making it a reliable solution for demanding injection molding applications.
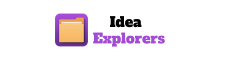
You must be logged in to post a comment Login